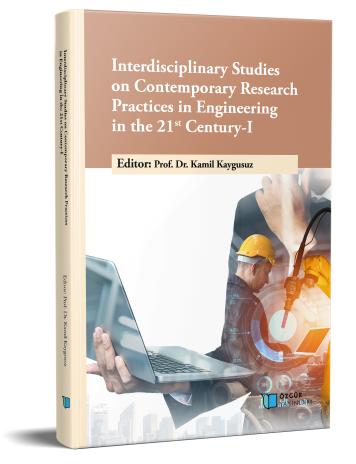
Comparison of Sustainable Cooling/Lubrication Conditions for Milling High-Strength S960 Steel
Chapter from the book:
Kaygusuz,
K.
(ed.)
2023.
Interdisciplinary Studies on Contemporary Research Practices in Engineering in the 21st Century- I.
Synopsis
The workpiece's tool life and surface integrity are very important in machining operations. Therefore, it is concluded that the improvement of the mentioned machinability parameters significantly affects production. One of the most important causes of rapid tool wear is the temperature at the tool-chip interface. To reduce the high temperatures in the cutting zone, conventional cutting fluid is used, which provides a cooling/lubricating effect at the tool-chip and tool-workpiece interfaces. However, traditional cutting fluids can cause some problems due to their high cost and harmful impact on the environment and human health. To eliminate these adverse conditions, environmentally friendly and economical alternative cooling/lubrication strategies are becoming more popular daily. This study investigated the milling of high-strength S960 steel under sustainable cooling/lubrication conditions and different machinability parameters. In this context, cryogenic-LN2 and minimum quantity lubrication (MQL) environments were compared. Cutting speeds were chosen as 125-250 m/min and feed rates of 0.15-0.25 mm/rev. During milling, cutting temperatures were measured with the help of a thermal camera, and the results were recorded. Then, tool wear and surface roughness analyzes were performed. According to the findings, it was determined that the best medium for surface roughness and the cutting temperature was cryo-LN2, and the best medium for tool flank wear was MQL cutting medium.